—專訪廣汽豐田有限公司總裝一部總裝技術1科科長 鐘裕民
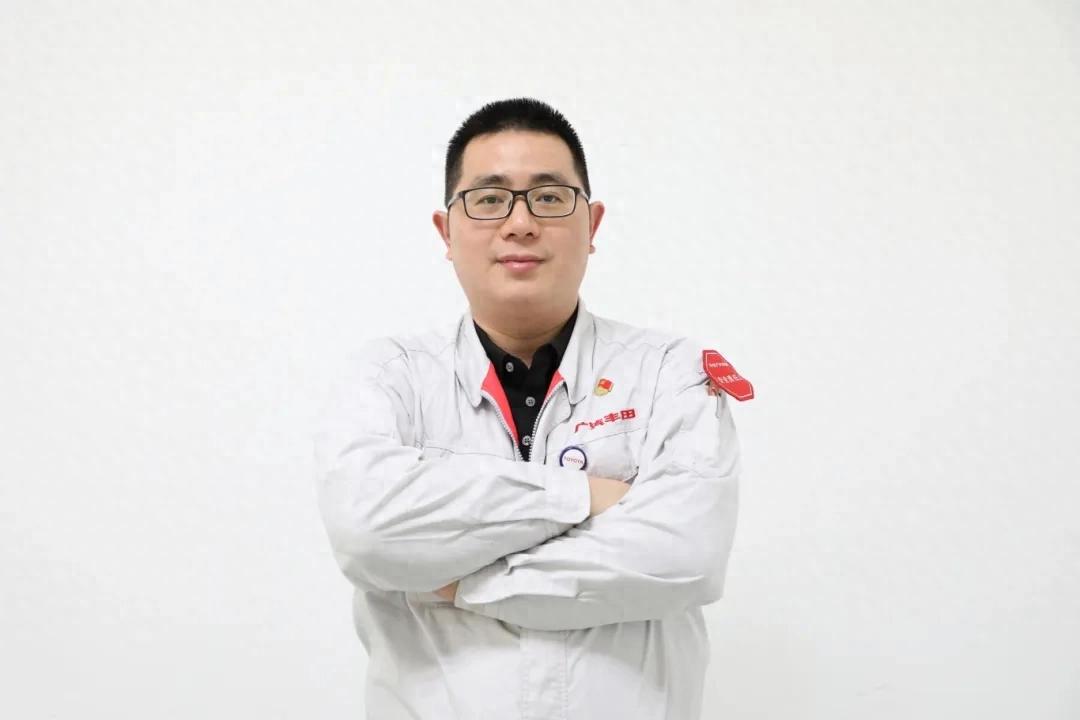
廣汽豐田有限公司總裝一部總裝技術1科科長 鐘裕民
企業介紹
廣汽豐田汽車有限公司(全文簡稱:廣汽豐田)成立于2004年9月1日,是由廣州汽車集團股份有限公司和豐田汽車公司各出資50%組建的合資企業。廣汽豐田扎根廣州南沙,具有粵港澳大灣區核心區位優勢。持續改善創新,始終保持穩健的高質量發展態勢,被譽為21世紀豐田全球模范工廠。
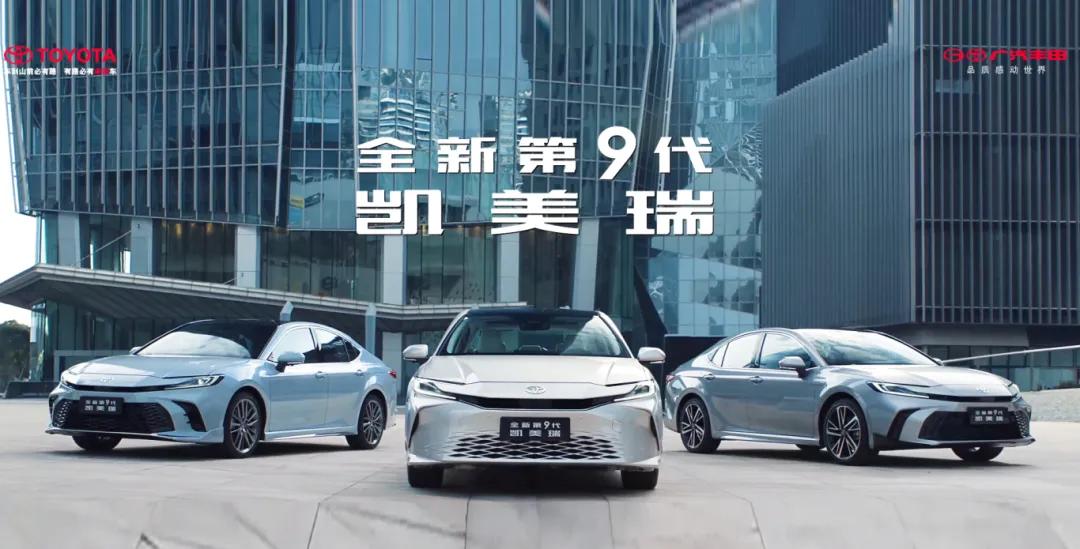
精益生產歷經多年的發展,已超越了單純的生產方式,成為一種先進的管理理念。汲取豐田精益管理的精髓,廣汽豐田的精益模式在中國的實踐已走過二十多個春秋,其發展路徑也在持續地優化與升級。在當今智能化浪潮的推動下,廣汽豐田與華章智能攜手合作,成功實現了多層穿梭車在動態汽車生產線上的首次應用。
PART.01
基于精益理念 不斷探索數智化新發展
豐田是全球領先的汽車制造商之一,其生產工藝和智能化優勢在全球汽車行業享有盛譽。其中“豐田生產方式”(Toyota Production System,TPS)旨在消除浪費、提高生產效率和質量管理。而TPS的核心理念主要涵蓋了Just In Time(JIT)和平準化管理體系,共同構成了精益物流供應體系的基礎,如今亦被各行各業的管理者們認可與采納。
廣汽豐田作為豐田全球的模范工廠,繼承了豐田數十年來汽車制造的精髓,自2004年成立以來,便以精益理念為核心,圍繞TPS、JIT和平準化原則,并引進了全球最先進的生產設備與工藝技術,在全球首次導入了全面的SPS模式(零部件分揀系統),實現了部品的選取和裝配的分離,極大地提升了生產效率和品質。構建了首條SPS模式(豐田物流分裝生產線),不斷提升裝配效率和質量。
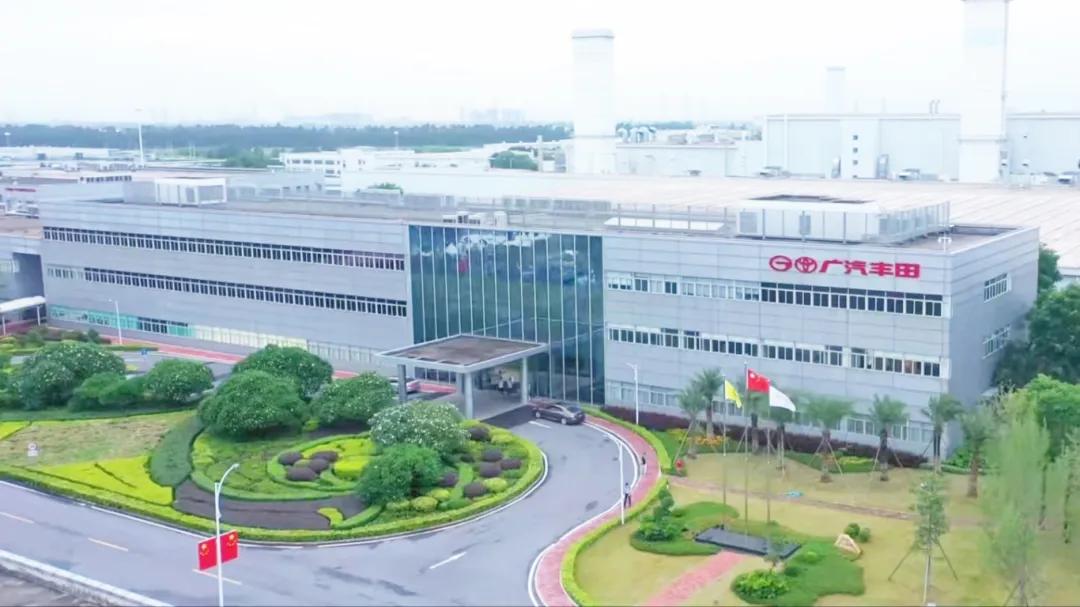
TPS的核心特點之一是以最終用戶的需求為生產起點,以拉動式生產模式實現作業流程最短化和庫存的最少化,因此廣汽豐田注重物流平衡,致力于實現零庫存。它要求企業實時反饋訂貨信息,從而促進生產與銷售環節的并行化運作,通過消除生產中的一切浪費來達到綜合降低成本的目標。
廣汽豐田伴隨著技術的進步不斷對這一理念進行優化,形成了當前的智能化高效物流系統。目前,廣汽豐田擁有5條生產線,年產能約為100萬臺,能夠同時生產超過十種不同車型,是豐田在全球范圍內規模化和集中化程度最高的生產基地之一,且生產線的效率已達到每58秒下線一輛車的驚人速度。主要銷售車型包括凱美瑞、漢蘭達、威蘭達、雷凌和塞納等,其2024年工業總產值有望達到1,500億元人民幣。
廣汽豐田總裝一部總裝技術1科科長鐘裕民表示,“我們運用了大數據、數字化、物聯網等先進技術,構建了供應商、廣汽豐田與顧客三位一體的智慧供應鏈體系,實現了低成本、短周期的零庫存柔性生產。廣汽豐田致力于為顧客提供高價值的產品、高品質的服務以及高品位的體驗,并將‘一切為了您的微笑’作為我們的企業使命。”
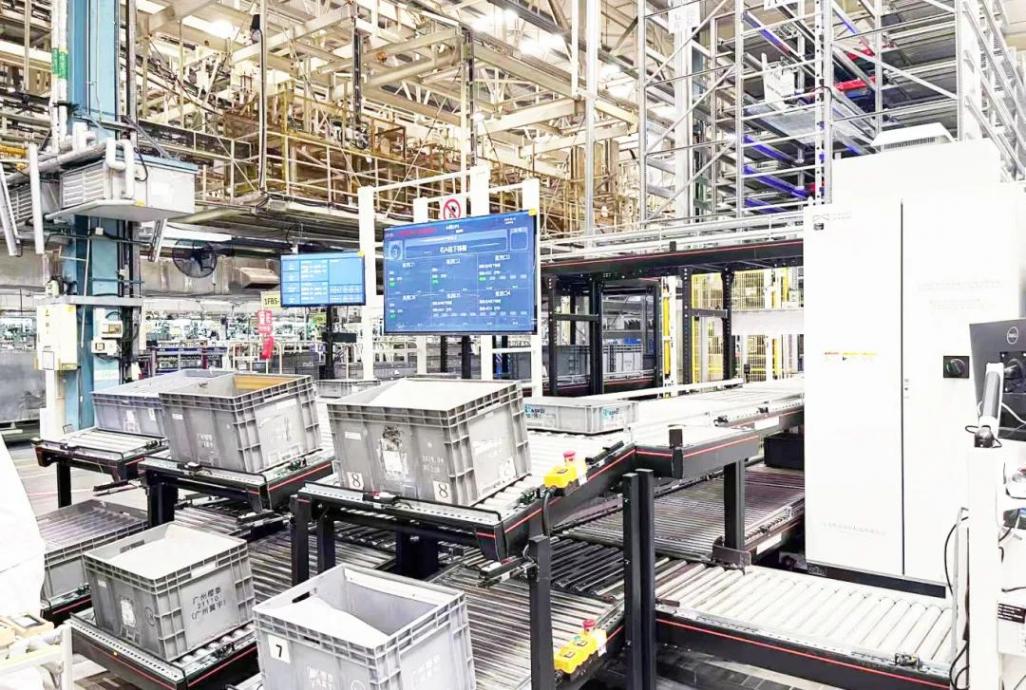
隨著中國物流領域不斷發展,廣汽豐田為積極應對中國市場變化,加深對智能化的理解與實踐,持續提升自身的綜合實力。在生產與物流管理過程中,結合IoT技術,廣泛采用機器人、無人運搬車等智能制造與智慧物流技術,不斷改進制造工藝和物流管理模式,提高生產效率和物流質量,降低企業成本,繼續引領汽車行業的發展。
PART.02
JIT技術背景下的柔性挑戰
廣汽豐田針對當前物流環境,構建了適應本地需求的物流體系。鑒于中國物流行業的迅猛發展和科技飛速進步,廣汽豐田深入考慮了中國國內的先進技術以及零部件倉儲企業的實踐經驗。結合豐田的核心理念,廣汽豐田進行了深入的本土化開發。
鐘裕民指出,與其他行業設立固定的倉儲中心不同,廣汽豐田在工廠內部實施了進度管控,從而形成了一個流動性更高的無倉儲管理體系。此外,豐田的SPS系統在管理上與其他行業存在顯著差異。在廣汽豐田的生產模式中,平準化概念得到了應用,并通過看板管理實現了先進先出的原則。在考慮倉儲概念時,廣汽豐田會遵循豐田的七大浪費原則,認為倉儲本質上是一種浪費。因此,如何根據這些原則消除浪費,并利用新技術來優化作業流程,正是廣汽豐田所面臨的挑戰。
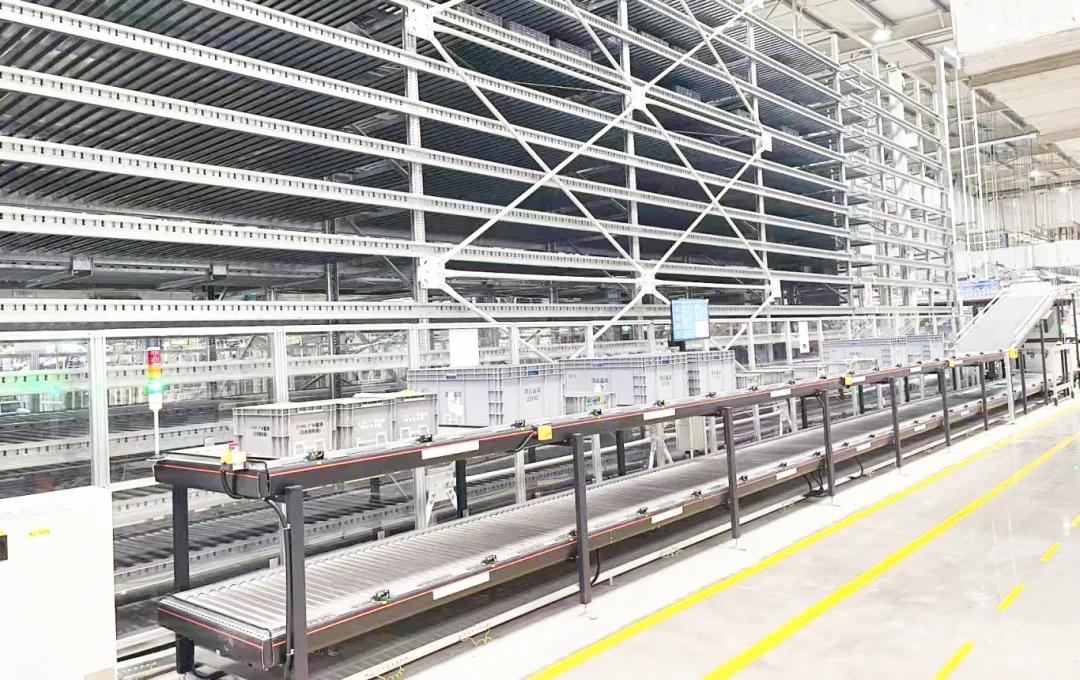
以穿梭車技術升級柔性產線
廣汽豐田的內部物流流程涵蓋了從P鏈或PC區到SPS以及生產線的各個環節。鑒于此,在推進創新改革的過程中,廣汽豐田根據當前的生產狀況,尋求適宜的技術解決方案,以實現更高層次的科技創新。特別是在SPS揀貨區域,傳統的人力循環揀貨方式導致了部品選取作業的效率低下。
針對這一問題,鐘裕民在一次行業展會上接觸到了多層穿梭車技術,并認識到其高效和靈活性的雙重優勢。相較于傳統的堆垛機,多層穿梭車的起貨效率更高,能夠適應豐田每58秒下線一輛車的生產節奏。同時,廣汽豐田的工廠內部實現了多車型的柔性生產,單條生產線的日吞吐量超過6萬箱,因此面對著繁多的SKU品種和復雜多樣的包裝容器。穿梭車技術的靈活調節功能正好能夠應對這些挑戰。“基于這兩個原則,我們開始探索如何將這種新技術與汽車生產流程中的各個環節相結合,并評估其應用的可行性。”
動態實施的需求
SPS作為一種向生產線提供單臺份成套零部件的配送方式,有效解決了從“一托”貨物到“一箱”貨物單位的轉變。然而,一旦貨物進入生產線,就需要按照單個單位進行流轉。廣汽豐田期望通過引入穿梭車技術,實現SPS供應流程中“一托”“一箱”與“一個”貨物存儲單位之間的高效轉換,滿足了生產線末端快速的需求。
鐘裕民強調道,“我們的整個生產鏈條非常敏感,任何異常都可能導致末端生產停滯。因此,動態實施過程對效率和準確度的要求極高。基于此,我們在項目需求上主要聚焦于實現高效、低成本和高精確度的三重目標。”
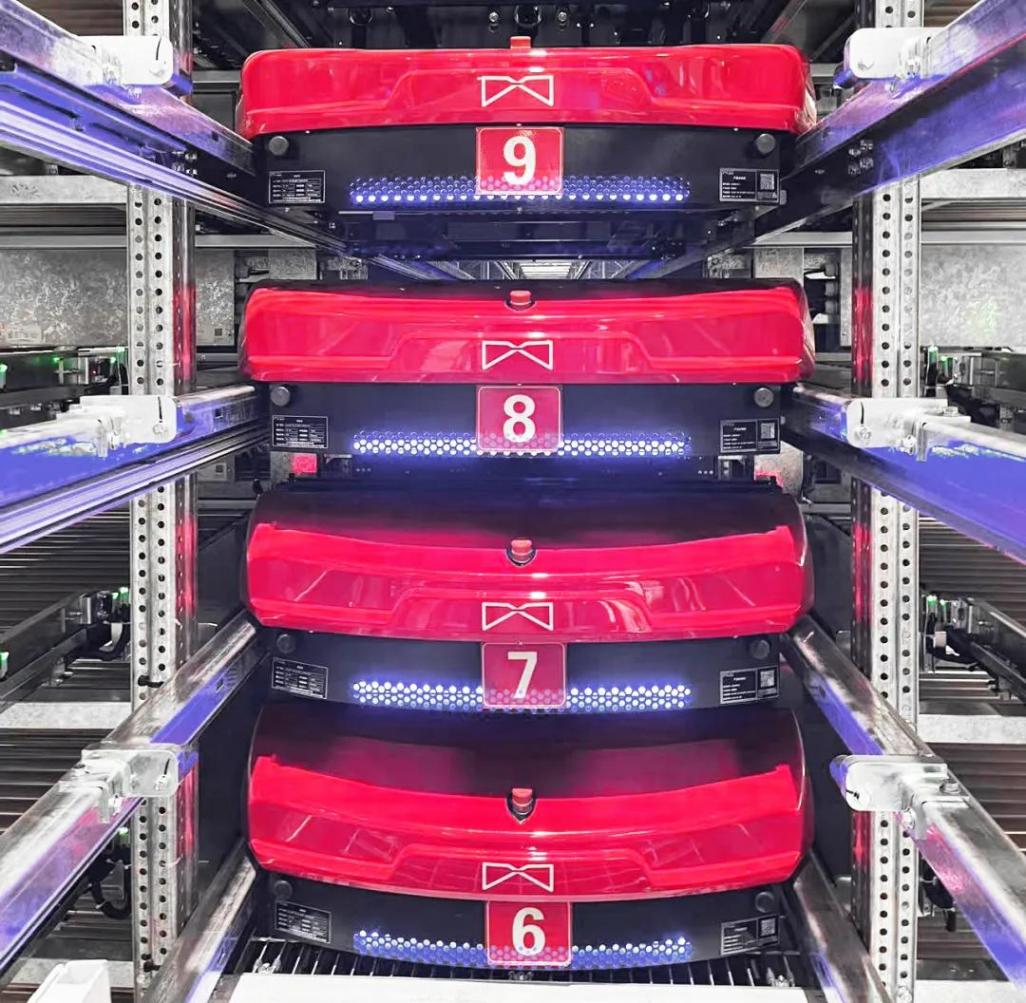
自2024年夏季起,廣汽豐田開始內部探討,旨在通過多層穿梭車的拆零揀選方式,并結合豐田的TPS理念與SPS的投入方式,制定一個既符合實際生產需求又高效的解決方案。實際上,穿梭車技術以往多應用于傳統倉儲項目,主要作為倉儲的功能,流通性低,而將其融入整車制造的生產環節,實現動態的高效流通,這在技術應用上尚屬于首次嘗試。
PART.03
攜手華章智能 打造高效智能物流體系
豐田的物流訂單與生產線分別由兩個獨立的系統進行管理。因此,解決方案需要一方面與外部物流系統相結合以實現訂單的入庫,另一方面則需與生產線的柔性生產系統相融合。基于這樣的需求,華章智能在深入研究豐田的生產方式后,為整個倉庫管理系統和揀貨系統開發了一套全新的系統。
“作為高速穿梭車領域的領導者,華章智能的產品效率在中國國內名列前茅,其團隊的專業性也極為突出。在實際案例考察中,我們發現華章智能的技術成熟度和產品穩定性都極為出色。在全面評估了華章智能的技術實力、行業定位、定制化服務能力以及管理協調能力后,我們最終決定選擇華章智能作為項目的合作伙伴。”鐘裕民在選擇華章智能作為合作伙伴時所依據的考量標準。
項目亮點彰顯技術優勢
據悉,該項目占地面積約300平方米,高度約6米,共14層,設有12個揀貨口,可實現兩側同時進行揀貨作業。該項目的優勢主要體現在以下三個方面。
首先,華章智能為廣汽豐田的立庫設計了回型線體,使貨物能夠快速完成揀選和回庫任務。同時,設置了撿貨指示系統,通過亮燈的模式幫助員工迅速對揀選貨物進行順序匹配,從而提高齊套配送產線的效率。
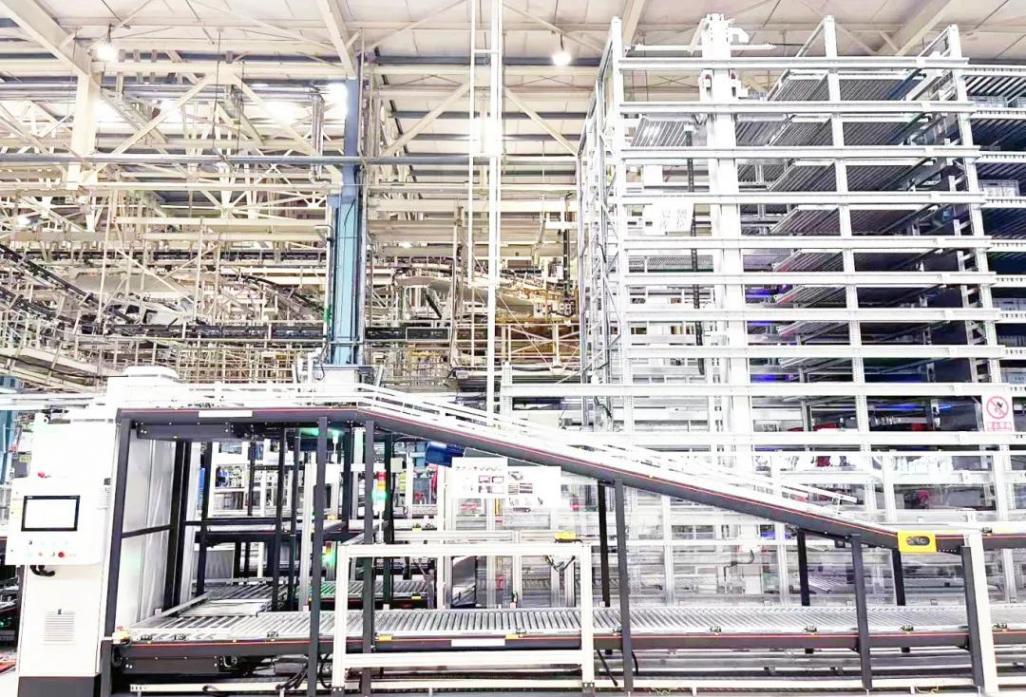
其次,華章智能在立庫每層均安裝了一臺高速穿梭車,并通過配置雙側提升機,在更小的占地面積內實現了更高的效率。值得一提的是,其單巷道可處理高達1,336箱/小時的流量。
此外,為滿足客戶需求,華章智能設計了多箱型混合存儲方案,并定制了可變式貨叉,以適應不同尺寸的箱體(最大尺寸為800*600,最小尺寸為340*280)。這一設計進一步節約了存儲空間,提高了企業的存儲密度,并增強了流程的靈活性。
在軟件開發方面,鑒于豐田生產系統與外部生產系統存在差異,它要求按照特定序列進行單件生產,這要求出貨也必須遵循相同的順序。華章智能在與客戶多次現場溝通后,特別定制開發了軟件,采用嚴格的排序方法來解決序列管理的難題。
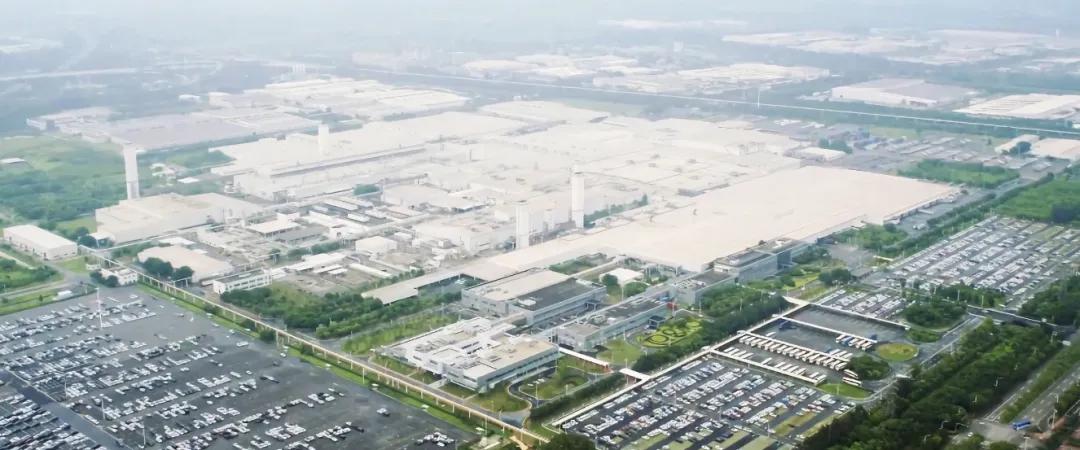
“在軟件的定制化開發方面,華章智能的工程師展現了極高的配合度。他們能夠迅速根據我們的需求提供反饋,并在實際運行測試中不斷識別并解決新出現的問題。”鐘裕民對華章智能的服務效率和響應速度給予了高度評價。
此外,廣汽豐田的電氣安全標準與中國國內安全體系有所不同,它比行業通用標準更為嚴苛,實際上是一個全球范圍內較為獨立的安全標準。因此,在項目實施過程中,華章智能面臨了多種安全標準的兼容挑戰,并進行了長時間的策略調整,以確保滿足廣汽豐田的安全要求。
技術革新下效率翻倍
從“一箱”到“一個”,廣汽豐田在首次引入立庫自動化技術取代傳統的人力揀選之后,實現了高效率、高精度的物流運搬和零件揀貨,既符合豐田TPS的生產理念,整體運行效果也達到預期目標,其中揀貨效率翻了一番,物流運轉效率則提高了約70%。
“我們與華章智能的合作也是對豐田物流體系進行現代化升級的一部分,通過引進中國國內的先進技術,不斷進行創新應用,以實現豐田物流模式在中國的本土化革新。”鐘裕民最后說道。